Most na rzece Drawie
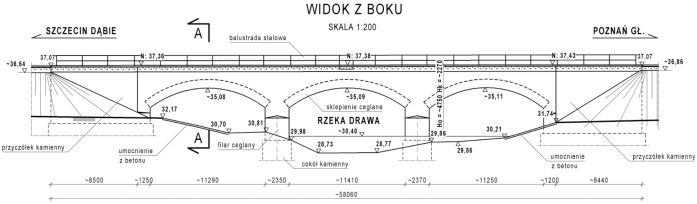
Nowy obiekt
Nowy obiekt został zaprojektowany jako jednoprzęsłowa, swobodnie podparta konstrukcja kratowa z przyczółkami żelbetowymi posadowionymi pośrednio na palach. Zaprojektowano osobne konstrukcje nośne pod każdy tor. Rozpiętość teoretyczna mostu wynosi 75,0 m, a szerokość konstrukcji nośnej dla każdego toru – 6,35 m. Szerokość całkowita ustroju nośnego dla jednego toru (łącznie z zewnętrznym chodnikiem dla obsługi) wynosi 7,25 m. Konstrukcję nośną przęsła stanowi stalowa kratownica o pasach równoległych z jazdą dołem. Rozstaw węzłów kratownicy wynosi 12,5 m. Pomost użytkowy mostu (na którym ułożone jest koryto balastowe torowiska) stanowi żelbetowa płyta o grubości 0,35 m oparta na poprzecznicach stalowych w rozstawie co 2,5 m. Całkowita wysokość konstrukcji wynosi 11,275 m, a osiowy rozstaw dźwigarów – 5,70 m. Posadowienie obiektu zaprojektowano w postaci fundamentu pośredniego – pali CFA.
Technologia montażu
Budowa mostu na rzece Drawie wymagała zastosowania nowoczesnych technologii i precyzji w działaniu. Jednym z kluczowych elementów tego projektu była zaawansowana technologia montażu konstrukcji stalowej w formie nasuwu podłużnego i poprzecznego. Dzięki temu podejściu udało się zrealizować pierwotny harmonogram robót, zachowując przy tym czynny tor kolejowy. Proces budowy mostu można podzielić na kilka kluczowych etapów:
- Scalanie konstrukcji: pierwszym etapem było scalanie konstrukcji w dostępnym miejscu w sąsiedztwie miejsca montażu, bezpośrednio na torze montażowym przeznaczonym do nasuwu. To wymagało precyzyjnego dopasowania i połączenia różnych elementów konstrukcji stalowej.
- Nasuwanie podłużne: po zakończeniu scalania i przygotowaniu podpór docelowych rozpoczęto proces nasuwu konstrukcji przez rzekę. Ten etap był kluczowy i wymagał wykorzystania siłowników hydraulicznych, które umożliwiły przesuwanie mostu na torze. Elementy konstrukcji spoczywały na ślizgach, które pozwalają na płynne przesuwanie się obiektu.
- Przesunięcie poprzeczne: kolejnym etapem było przesunięcie poprzeczne obiektu. W tym celu zamontowano specjalne ślizgi poprzeczne i usunięto ślizgi podłużne. Przesunięcie to było niezwykle precyzyjne i wymagało zastosowania przelotowych siłowników hydraulicznych oraz prętów ze stali o wysokiej wytrzymałości.
- Podpory tymczasowe i podniesienie: po przesunięciu konstrukcji na podpory tymczasowe, zlokalizowane w bezpośrednim sąsiedztwie podpór docelowych, wybudowano cztery podpory kratowe. Pełniły one kluczową rolę przy podniesieniu obiektu na odpowiednią wysokość, co umożliwiło montaż kształtownika, po którym konstrukcja została nasunięta w miejsce docelowe.
- Nasuwanie w miejsce docelowe: ostatnim etapem było nasuwanie konstrukcji w miejsce docelowe. To zrealizowano również z pomocą przelotowych siłowników hydraulicznych oraz prętów wysokowytrzymałych. Po przesunięciu poprzecznym konstrukcja została opuszczona na docelową pozycję.
Zastosowanie technologii nasuwu podłużnego i poprzecznego przy czynnym torze było jedyną możliwością zachowania funkcjonalności trasy kolejowej podczas prac budowlanych. Dzięki tej zaawansowanej technologii możliwe były jednoczesne scalanie konstrukcji, rozbiórka części istniejącego mostu oraz wykonanie podpór dla nowego obiektu. To także umożliwiło montaż deskowania i zbrojenia płyty pomostu przed jej nasunięciem, co przyspieszyło cały proces budowy.
Komentarz firmy
Ireneusz Merchel, prezes Zarządu PKP Polskich Linii Kolejowych S.A.
Most kolejowy nad Drawą na linii kolejowej nr 351 Poznań Główny – Szczecin Główny został wybudowany w ramach projektu „Prace na linii kolejowej E59 na odcinku Wronki Słonice” dofinansowanego ze środków unijnych instrumentu CEF („Łącząc Europę”). W tym przypadku most dosłownie łączy także dwa województwa – wielkopolskie i lubuskie, których granica przebiega na rzece Drawie. Obiekt zastąpił dotychczasową, przedwojenną, konstrukcję trzyprzęsłową w formie sklepionej wykonaną z cegły i kamienia. Nowy most uwzględnia aktualne wymagania przeciwpowodziowe. Został pozbawiony podpór nurtowych (stare całkowicie rozebrano) i wykonany jako jednoprzęsłowy. Konstrukcja w formie kratownicy stalowej została podparta na przyczółkach żelbetowych posadowionych pośrednio na palach. Wykonano dwa niezależne ustroje nośne – osobno dla każdego z torów, co ułatwi w przyszłości prace utrzymaniowe i remontowe.
Pod obiektem, wzdłuż umocnionego gabionami koryta rzeki, zastosowano rozwiązania ekologiczne – utworzono przejście dla dużych i małych zwierząt, gdyż most znajduje się w otoczeniu lasów na obszarze Natura 2000.
Z uwagi na rozpiętość wynoszącą 75,0 m i sztywność konstrukcji zabudowano tzw. przyrządy wyrównawcze niwelujące wpływ naprężeń i przemieszczeń przy współpracy obiektu z torem.
Całość prac była prowadzona przy czynnym ruchu kolejowym. Na każdym etapie budowy regularny ruch pociągów pasażerskich i towarowych odbywał się po sąsiednim czynnym torze. Najbardziej newralgiczne prace były prowadzone podczas tzw. „domknięć nocnych”, tj. czasowych nocnych przerw w ruchu pociągów trwających maksymalnie 4 godziny. Dla bezpieczeństwa wyłączano także napięcie w całej sekcji sieci trakcyjnej.
Należy podkreślić, że okres budowy przypadł na czas pandemii COVID-19 oraz wybuchu wojny w Ukrainie, co skutkowało m.in. zaburzeniami na rynku materiałów budowlanych. Dzięki prowadzonemu przez PKP Polskie Linie Kolejowe S.A. ciągłemu monitoringowi rynku materiałów strategicznych dla realizacji programów inwestycyjnych oraz doświadczeniu i wiarygodnej pozycji wykonawcy dostawy materiałów na obiekt zostały zrealizowane bez istotnych przeszkód, co umożliwiło zakończenie budowy i oddanie mostu do eksploatacji.
---------------------------------------------------------------------------------------------
Piotr Olejnik, Kierownik Robót Mostowych, PORR S.A.
Pierwotne założenia projektowe, dostępne na etapie przetargu, przewidywały całkowite wyłączenie z ruchu linii kolejowej na kilka tygodni. Był to czas przewidziany na wykonanie operacji technologicznych związanych z rozbiórką istniejących obiektów jednoprzestrzennych i montażu konstrukcji nośnej nowego obiektu pod jednym torem.
Z uwagi na istotne znaczenie strategiczne i gospodarcze LK351 jedyną możliwością okazało się zamknięcie jednego toru i prowadzenie robót w systemie połówkowym przy czynnym torze.
Ze względu na kolizję projektowanego mostu z mostem istniejącym konieczna była rozbiórka części podpór obiektu oraz konstrukcji nośnej w miejscu umożliwiającym wykonanie nowej konstrukcji jednego toru przy czynnym ruchu na torze drugim. Istniejący obiekt był konstrukcją jednoprzestrzenną, a scalenie konstrukcji w bezpośrednim sąsiedztwie czynnego toru i trakcji elektrycznej było niemożliwe.
Należało zatem sprawdzić, czy możliwa jest częściowa rozbiórka konstrukcji, tak aby most zachował nośność dla ruchu pociągów. Okazało się, że jakakolwiek dokumentacja archiwalna jest niedostępna i konieczne było wykonanie odkrywek w celu ustalenia konstrukcji i nośności obiektu.
Zastosowanie technologii nasuwu podłużnego i poprzecznego przy czynnym torze było jedyną możliwością realizacji pierwotnego harmonogramu robót. Technologia ta umożliwiła jednoczesne scalanie konstrukcji, rozbiórkę części istniejącego mostu oraz wykonanie podpór mostu projektowanego. Możliwy był również montaż deskowania i zbrojenia płyty pomostu przed jej nasunięciem.
Dzięki fachowej pracy całego zespołu PORR S.A. pomimo wielu zmiennych udało nam się ukończyć to znaczące przedsięwzięcie inżynieryjne w terminie.
---------------------------------------------------------------------------------------------
Krzysztof Grej, Egis
Most przez Drawę stanowi jeden z większych obiektów inżynieryjnych, jakie są zlokalizowane na modernizowanej linii kolejowej nr 351: Poznań Główny – Szczecin Główny.
Zasadniczym warunkiem realizacyjnym, który musiał być brany pod uwagę przez projektanta na etapie prac projektowych, była konieczność zaprojektowania konstrukcji spełniającej następujące wymogi:
- rozdzielenie konstrukcji nośnej dla każdego toru w celu umożliwienia utrzymywania ruchu na jednym torze,
- zastosowanie takiej rozpiętości (światła) obiektu, aby „okraczyć” istniejący obiekt i dodatkowo zapewnić obustronne przejścia dla zwierząt o szerokości minimum 10,0 m na każdym brzegu rzeki.W celu spełnienia tych wymogów zaprojektowano jednoprzęsłowy most o konstrukcji kratowej z jazdą dołem i rozpiętości przęsła 75,0 m.
Takie rozwiązanie umożliwiło montaż nowej konstrukcji nośnej nawet przed całkowitą rozbiórką konstrukcji istniejącego mostu.
Z punktu widzenia projektowego obiekt posiada dwa ciekawe rozwiązania techniczne, rzadziej spotykane w polskiej „rzeczywistości” obiektów kolejowych.
Pierwszą sprawą jest sposób łożyskowania obiektu. Zastosowano tu oparcie każdej kratownicy na czterech łożyskach wielokierunkowo przesuwnych przenoszących tylko siły pionowe (od obciążeń stałych i ruchomych). Natomiast do przenoszenia sił poziomych (pochodzących od sił hamowania, obciążeń wiatrowych i uderzeń bocznych taboru) zastosowano łożysko blokujące (łożysko stałe) i łożysko prowadzące (jednokierunkowo przesuwne). Łożyska blokujące i prowadzące są zlokalizowane w osi podłużnej każdej konstrukcji nośnej i przymocowane do skrajnych poprzecznic podporowych. W celu przeniesienia sił poziomych z tych łożysk na dźwigary poprzecznice skrajne mają przekroje skrzynkowe, a dochodzące do osi poprzecznicy dolne stężenia kraty typu K mają specjalnie wzmocnione przekroje poprzeczne.
Drugim zagadnieniem jest sposób wykonstruowania żelbetowej płyty torowiska. W celu uniknięcia generowania dużych sił podłużnych pochodzących od efektów termicznych (różnicy temperatur płyta betonowa – konstrukcja stalowa) płytę podzielono na trzy segmenty o długości 25,0 m każdy. Pomiędzy segmentami płyty zastosowano dylatacje poprzeczne. Każdy segment płyty został zespolony z poprzecznicą węzłową kraty zlokalizowaną w środku każdego segmentu. Na pozostałych poprzecznicach oparta jest płyta z możliwością przesuwu. W celu zastabilizowania poprzecznych ruchów płyty na końcach każdego segmentu zaprojektowano „opórki” w dźwigarze stalowym, do których za pomocą łożysk elastomerowych mocowane są naroża każdego segmentu płyty.
Budowa obiektu przebiegła bardzo sprawnie. W trakcie trwania prac potrzeba kontaktów pomiędzy projektantem a wykonawcą była ograniczona do formalnego minimum. Świadczy to wysokim profesjonalizmie wykonawcy, ale i o prawidłowo sporządzonej dokumentacji technicznej.
Mogą zainteresować Cię również
Wywiady
Zbigniew Tabor: Aby zarządzać drogami, potrzebna jest wizja
Z perspektywy Pańskiej długoletniej pracy na stanowisku dyrektora, jakie lekcje życiowe wyniósł Pan z tego doświadczenia i w jaki sposób wpłynęły one na Pana podejście do życia? Zbigniew Tabor: Przekonałem się, że sprawy techniczne, jakości robót, technologii oraz zagadnienia prawne związane z prawem zamówień publicznych, ustawą o drogach public...
KPO: wsparcie unijne dla polskiej odbudowy
KPO to strategiczny program przyjęty przez rząd Polski, który ma na celu odbudowę gospodarki oraz zwiększenie jej odporności na wszelkie kryzysy. Program składa się z 55 inwestycji i 55 reform, których celem jest stymulowanie wzrostu gospodarczego, tworzenie miejsc pracy oraz modernizacja i transformacja różnych sektorów gospodarki. Środki na realizację KPO pochodzą głównie z funduszy Unii Europejskiej, które zostały przyznane Polsce w ramach tzw. Planu Odbudowy dla Europy. Polska otrzyma 59,...
Stan techniczny urządzeń obcych w kontekście trwałości konstrukcji mostowych – na podstawie własnych doświadczeń z przeglądów i diagnostyki
Nakłada się na to kształt elementów konstrukcyjnych mostów, rozstaw poprzecznic, żeberek usztywniających, wsporników chodnikowych i tym podobnych elementów. Dlatego też odpowiednie mocowania i prowadzenia przez obiekt tych ważnych z punktu widzenia odbiorców mediów powinny być rozwiązywane, projektowane, a następnie instalowane z należytą starannością techniczną. Zdaniem autorów w tym procesie powinien uczestniczyć zespół interdyscyplinarnych zainteresowanych tematem specjalistów zarówno z gr...
Jednonaczyniowe koparki hydrauliczne
Podział koparek jednonaczyniowych ze względu na wielkość naczynia roboczego i przeznaczenie [2]: uniwersalne (budowlane) – pojemność łyżki do 2 m3, odkrywkowe – pojemność łyżki: 3-10 m3, nadkładowe – pojemność łyżki: 4-140 m3, zgarniakowe – pojemność łyżki: 4-180 m3. Podział według rodzaju osprzętu [2]: koparka z osprzętem przedsiębiernym (nadsiębiernym) – koparka przedsiębierna (nadsiębierna), koparka z osprzętem podsiębiernym – koparka podsiębierna, koparka z osprzętem zgarniakowym (zabiera...
Rodzaje warstw mieszanki mineralno-asfaltowej oraz zasady ich wykonywania i wbudowania
Wykonanie uszorstnienia w przypadku MMA polega na mechanicznym naniesieniu w odpowiednim czasie na gorącą warstwę ścieralną posypki i wgnieceniu jej walcami w czasie zagęszczania. W miejscach trudno dostępnych nakładanie posypki może odbywać się ręcznie. Niezwiązaną posypkę po ostygnięciu warstwy należy usunąć szczotką mechaniczną. Przy wyborze uziarnienia należy kierować się wymaganiami ochrony przed hałasem. Jeżeli wymaga się zmniejszania hałasu od kół pojazdów, np. na terenach zurbanizowan...
Co trzeba wiedzieć o cesji umowy leasingu
Czy wiesz, że istnieje skuteczny sposób na pozbycie się problemów związanych z realizacją umowy leasingu? W artykule omówiono, dlaczego przejęcie leasingu poprzez cesję umowy może być najlepszym rozwiązaniem dla wszystkich zaangażowanych stron. Odkryj korzyści płynące z tego procesu i przekonaj się, dlaczego jest to preferowany sposób przedterminowego rozliczenia umowy leasingowej. Umowy leasingu są zawierane na określony czas i nie przewidują możliwości rozwiązania umowy przed terminem. Jedn...
O obliczeniach dynamicznych konstrukcji mostowych
Analiza modalna Pełna analiza modalna obejmuje wyznaczenie współczynników tłumienia, rozprzęganie układu równań ruchu opisującego dynamikę modelu i identyfikację własności dynamicznych obiektu. Dzieli się na analizę modalną teoretyczną, eksperymentalną i eksploatacyjną. Zagadnienie drgań własnych można utożsamiać z teoretyczną analizą modalną, która stanowi część znacznie szerszej analizy dynamicznej określanej w literaturze jako analiza modalna [3, 4, 11]. Rozwiązanie zagadnienia własnego po...
Zabezpieczenia szczelin dylatacyjnych w mostach
Szczeliny dylatacyjne są kluczowym elementem w konstrukcjach mostowych, zapewniającym skuteczne zarządzanie odkształceniami, ruchem pojazdów oraz odprowadzaniem wody. Przestrzeganie norm i wytycznych, zawartych m.in. w WR-M-71 Katalog typowych elementów i urządzeń wyposażenia drogowych obiektów inżynierskich, jest kluczowe w celu zapewnienia ich niezawodności. Szczeliny dylatacyjne w infrastrukturze mostowej odgrywają kluczową rolę w zapewnieniu bezpieczeństwa i trwałości konstrukcji. W celu ...
Ronda ‒ problematyka uszkodzeń nawierzchni
Wytyczne i realia użytkowania W obecnie stosowanych wytycznych do projektowania [7] znajdują się m.in. zapisy: „Szerokości jezdni i pierścienia ronda jednopasowego powinny zapewniać przejezdność pojazdu miarodajnego”. Zdaniem autorów, przyjmując założenie, że pojazd miarodajny (np. pojazd ciężarowy z naczepą) będzie poruszał się po przejezdnym pierścieniu, zgodnie z zapisami ustawy o drogach publicznych [9] należy uznać pierścień jako część jezdni przeznaczonej do ruchu. Takie założenie wynos...
Kraków: Tunel wzdłuż Opolskiej otwarty dla ruchu.
Od 22 maja tunel wzdłuż Opolskiej – jeden z najważniejszych obiektów inżynierskich budowanych w ramach linii KST III do Górki Narodowej – dostępny jest w całości dla kierowców. Ma dwie niezależne komory, każda po dwa pasy ruchu, jest długi na ok. 100 metrów, jest w stanie przyjąć pojazdy ważące nawet do 50 ton. Przypomnijmy: budowa tunelu rozpoczęła się w marcu 2022 r. od wykonania murków prowadzących dla ponad 60 tonowego dźwigu z wybierakiem. Maszyna sukcesywnie – metr za metrem – wybierała...
Kalendarium
Relacje
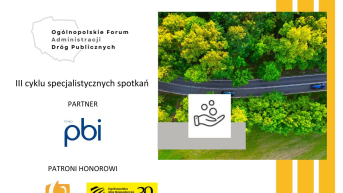
III Ogólnopolskie Forum Administracji Dróg Publicznych – Zastosowanie kruszyw i materiałów w inwestycjach na drogach gminnych, powiatowych i wojewódzkich
9 maja 2024 r. odbyło się trzecie spotkanie III cyklu Ogólnopolskiego Forum Administracji...
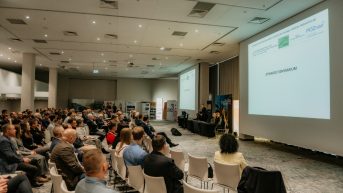
II (32) SEMINARIUM „MOSTY. BUDOWA, WZMACNIANIE, PRZEBUDOWA”
W dniach 18 - 19.04.2024 roku w Poznania odbyło się seminarium...
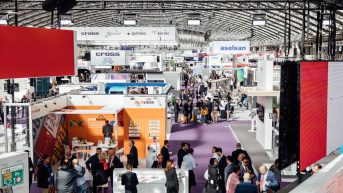
Intertraffic Amsterdam 2024 – ekosystem stworzony dla przyszłej mobilności
Intertraffic Amsterdam, wiodące na świecie wydarzenie branżowe w zakresie infrastruktury,...

Novdrog 2024
17-19 kwietnia br. w Niepołomicach odbyła się Konferencja Naukowo-Techniczna „Nowoczesne ...