Wykorzystanie granulatu asfaltowego − cykl życia mieszanki mineralno-asfaltowej
Właściwości mieszanki
W trakcie produkcji, transportu oraz wbudowania mieszanki dochodzi do niewidocznych gołym okiem zmian składu chemicznego lepiszcza asfaltowego użytego do produkcji mieszanek. Wraz ze zmianą składu chemicznego następuje zmiana właściwości asfaltu, a finalnie także mieszanki mineralno-asfaltowej. Proces starzenia się asfaltu od początku wykorzystania mieszanek mineralno-asfaltowych jest obecny, a jego wpływ jest obserwowany i badany od dziesiątek lat. Pod wpływem termooksydacji następuje gwałtowne starzenie technologiczne mieszanki wpływające przede wszystkim na właściwości lepiszcza asfaltowego poprzez zmiany zawartości frakcji asfaltu, którymi są:
- asfalteny,
- żywice,
- oleje aromatyczne,
- oleje nasycone.
Właściwości mieszanki zmieniają się poprzez ulatnianie się lekkich frakcji asfaltu oraz utlenianie części związków chemicznych, przez co uzyskują one większą masę molekularną. Oba te zjawiska wpływają na stosunkowe zwiększenie ilości związków budujących frakcje żywiczne i asfaltowe, powodujące wzrost sztywności lepiszcza asfaltowego oraz przesunięcie zakresu temperaturowego jego lepkosprężystej pracy (obniżenie penetracji, wzrost temperatury mięknienia), finalnie sprawiając, że asfalt i mieszanka są twardsze i bardziej kruche, zmniejszając szansę na powstawanie kolein, jednak zwiększając prawdopodobieństwo wystąpienia spękań termicznych i zmęczeniowych.
Eksploatacja nawierzchni
W okresie eksploatacji nawierzchni, podobnie jak w czasie produkcji mieszanki mineralno-asfaltowej, dochodzi do procesów starzenia lepiszcza asfaltowego. Starzenie to jest uzależnione od dostępu do powietrza (tlenu) oraz od temperatury, a jego przebieg jest znacznie wolniejszy od przebiegu starzenia podczas procesów produkcyjnych. Należy jednak pamiętać, że starzenie się nawierzchni drogowej w dalszym ciągu zachodzi, a proces ten przebiega nierównomiernie.
Najbardziej narażoną na starzenie warstwą nawierzchni jest warstwa ścieralna. Przyjmuje się, że jedynie w przypowierzchniowej części warstwy ścieralnej dochodzi do intensywnych procesów starzenia, ze względu na nieograniczony dostęp tej części nawierzchni do tlenu oraz ekspozycję na promieniowanie ultrafioletowe ze względu na nasłonecznienie nawierzchni. Informacja ta została potwierdzona w badaniach naukowych [9]. W konsekwencji to w warstwie ścieralnej dochodzi do reakcji, które mogą prowadzić do mikrospękań i do zwiększania dostępu do tlenu w głąb warstwy ścieralnej, następnie do dalszej degradacji nawierzchni.
Pozostałe warstwy asfaltowe również podlegają stopniowemu starzeniu, ale proces ten przebiega wyraźnie łagodniej ze względu na brak ekspozycji na promieniowanie UV. Obecnie laboratoryjne metody starzeniowe uwzględniają jedynie wpływy temperatury oraz utleniania lepiszcza, pomijając występowanie w rzeczywistych warunkach promieniowania, które w znaczący sposób oddziałuje na właściwości warstwy ścieralnej. Efekty starzenia pod wpływem promieniowania UV są zbliżone do termooksydacyjnych, postępują jednak bardziej agresywnie.
Po okresie eksploatacji nawierzchni następuje konieczność remontu lub przebudowy nawierzchni drogowej. Jednym z najczęstszych zabiegów przeprowadzanych w takiej sytuacji jest wymiana warstw asfaltowych. W wariancie najmniej inwazyjnym jest to wymiana warstwy ścieralnej, która najczęściej odbywa się przy użyciu frezarek specjalnie do tego przeznaczonych. Jeśli warstwa ścieralna charakteryzowała się brakiem remontów cząstkowych (łaty, powierzchniowe utrwalenie), to tak pozyskany destrukt asfaltowy charakteryzuje się wysoką wartością. Wynika to z faktu, że jest dobrze uziarniony, a lepiszcze asfaltowe pochodzi z jednego źródła. Destrukt ten wymaga przebadania pod kątem uziarnienia po frezowaniu (proces frezowania powoduje wzrost zawartości frakcji pylastej na skutek niszczenia części ziaren kruszywa) oraz pod kątem właściwości lepiszcza odzyskanego (badania temperatury mięknienia oraz penetracji). Następnie taki destrukt, jeśli spełnia wszystkie wymogi, może kwalifikować się bez dodatkowego procesu obróbki jako granulat asfaltowy lub można poddać go procesom obróbki, np. procesowi granulacji. Finalnie granulat asfaltowy może być wykorzystany do produkcji nowych mieszanek mineralno-asfaltowych.
Przebudowy i remonty nawierzchni
W przypadku przebudowy nawierzchni lub bardziej rozbudowanego remontu może dojść do konieczności wymiany wszystkich warstw asfaltowych. Wówczas istotne jest, aby dobrze zaplanować proces rozbiórki tych warstw. Przed wykonaniem rozbiórki warto pobrać z nawierzchni próbki warstw asfaltowych w celu określenia ich składu ziarnowego oraz właściwości lepiszcza. W zależności od przyszłego przeznaczenia destruktu asfaltowego należy odpowiednio dobrać metodę jego pozyskania. W przypadku wykorzystania destruktu do umocnienia poboczy nie są wymagane szczególne zabiegi poza uzyskaniem odpowiednich frakcji samego destruktu asfaltowego. Destrukt pozyskany w celu zastosowania do mieszanek na zimno (w Polsce to najczęściej mieszanka mineralno-cementowo-emulsyjna, MCE) powinien mieć zweryfikowane właściwości, jednak również w tym przypadku kluczowe są jego uziarnienie oraz zawartość lepiszcza. Najwięcej uwagi powinno zostać poświęcone na pozyskanie destruktu asfaltowego w celu wykorzystania go do mieszanek mineralno-asfaltowych.
Każda rozbierana warstwa powinna być frezowana oddzielnie tak, aby dana partia destruktu asfaltowego była jednorodna. Warstwy zawierające asfalt drogowy powinny być frezowane oddzielnie od warstw z asfaltem modyfikowanym, ponadto powinno następować frezowanie warstw oddzielnie również ze względu na uziarnienie. Granulat asfaltowy pochodzący z warstwy ścieralnej zazwyczaj charakteryzuje się uziarnieniem do 11 mm (dawniej 12,8 mm), co sprawia, że możliwości jego zastosowania są inne od granulatu o uziarnieniu do 22 mm pochodzącego z warstwy podbudowy zasadniczej. W rzeczywistości jednak ze względu na ograniczone możliwości magazynowe wytwórni oraz ze względu na potrzebę skrócenia procesu rozbiórki wszystkie warstwy są frezowane w jednym procesie.
Finalnie granulat asfaltowy powinien być jednorodny pod kątem uziarnienia kruszywa mieszanki, zawartości lepiszcza, rodzaju lepiszcza, a najlepiej także rodzaju skały wykorzystanej do produkcji mieszanki. To wszystko pozwala na uzyskanie największych korzyści ze stosowania materiału z recyklingu, jakim jest granulat asfaltowy.
Wykorzystanie granulatu asfaltowego do produkcji mieszanek mineralno-asfaltowych może się odbywać za pomocą dwóch metod − „na zimno” oraz „na gorąco” (rys. 1, rys. 2). Metoda „na zimno” jest obecnie w Polsce szeroko rozpowszechniona, nie wymaga skomplikowanych instalacji i polega na dozowaniu granulatu asfaltowego o temperaturze otoczenia (bez podgrzewania) bezpośrednio do mieszalnika wytwórni, gdzie styka się z gorącym kruszywem. Obecnie dopuszczone jest jednak stosowanie maksymalnie 20% granulatu asfaltowego w stosunku do masy gotowej mieszanki w metodzie „na zimno” według Wymagań Technicznych WT-2. Jest to związane między innymi z problemami z wilgotnością granulatu asfaltowego, która może spowodować zaburzenia w pracy sortownika poprzez unoszącą się parę wodną powstałą przy zetknięciu się gorącego kruszywa z wilgotnym granulatem asfaltowym.
Galeria
Mogą zainteresować Cię również
Wywiady
Kamila Czaja: Zero tolerance for compliance
Jakie są priorytety firmy w obszarze zrównoważonego rozwoju i ochrony środowiska naturalnego? Czy firma planuje podejmować konkretne działania w celu osiągnięcia neutralności klimatycznej? Kamila Czaja: Jako firma zdecydowaliśmy się zobowiązać do przestrzegania Porozumienia Paryskiego (Paris Agreement), tj. międzynarodowego traktatu dotyczącego ...
Edukacja surowcowa elementem bezpieczeństwa surowcowego państwa
Jaki jest stan wiedzy nt. branży wydobywczej? Potwierdzeniem dla powyżej sformułowanych stwierdzeń mogą być wyniki ankiety przeprowadzonej wśród uczniów w trzech kategoriach wiekowych: < 10 lat, 10-15 lat oraz > 15 lat. Łącznie otrzymano 1000 ankiet, z czego ponad 700 ankietowanych to młodzież powyżej 10. roku życia. Celem było pozyskanie ogólnej wiedzy na temat stosunku dzieci i młodzieży do branży wydobywczej oraz edukacji surowcowej przy obecnej podstawie programowej w szkołach podst...
Stan techniczny urządzeń obcych w kontekście trwałości konstrukcji mostowych – na podstawie własnych doświadczeń z przeglądów i diagnostyki
Nakłada się na to kształt elementów konstrukcyjnych mostów, rozstaw poprzecznic, żeberek usztywniających, wsporników chodnikowych i tym podobnych elementów. Dlatego też odpowiednie mocowania i prowadzenia przez obiekt tych ważnych z punktu widzenia odbiorców mediów powinny być rozwiązywane, projektowane, a następnie instalowane z należytą starannością techniczną. Zdaniem autorów w tym procesie powinien uczestniczyć zespół interdyscyplinarnych zainteresowanych tematem specjalistów zarówno z gr...
Jednonaczyniowe koparki hydrauliczne
Podział koparek jednonaczyniowych ze względu na wielkość naczynia roboczego i przeznaczenie [2]: uniwersalne (budowlane) – pojemność łyżki do 2 m3, odkrywkowe – pojemność łyżki: 3-10 m3, nadkładowe – pojemność łyżki: 4-140 m3, zgarniakowe – pojemność łyżki: 4-180 m3. Podział według rodzaju osprzętu [2]: koparka z osprzętem przedsiębiernym (nadsiębiernym) – koparka przedsiębierna (nadsiębierna), koparka z osprzętem podsiębiernym – koparka podsiębierna, koparka z osprzętem zgarniakowym (zabiera...
Nawierzchnie drogowe. Warianty konstrukcyjne
Nawierzchnie podatne i półsztywne z warstwą nawierzchniową z mieszanki niezwiązanej W skład konstrukcji nawierzchni podatnej lub półsztywnej z warstwą nawierzchniową z mieszanki niezwiązanej wchodzą: Warstwa nawierzchniowa Podbudowa zasadnicza Podbudowa pomocnicza Warstwa mrozoochronna Schemat i nazwy tych warstw konstrukcji nawierzchni podatnych i półsztywnych z warstwą nawierzchniową z mieszanki niezwiązanej są przedstawione w tab. 3. Ten schemat stanowi podstawę dla projektowania i budowy ...
Zasady organizacji ruchu drogowego
Uproszczony projekt organizacji ruchu Możliwe jest dopuszczenie przez urząd zarządzający ruchem zmian w organizacji ruchu na podstawie projektu uproszczonego, dotyczy to robót związanych z utrzymaniem drogi niewymagających całkowitego zamknięcia jezdni dla ruchu pojazdów samochodowych, które wymagają zmian w organizacji ruchu tylko w czasie wykonywania czynności. Zatwierdzanie organizacji ruchu Organizację ruchu zatwierdza, na podstawie złożonego projektu organizacji ruchu, organ zarządzający...
Najczęstsze błędy projektowe i wykonawcze ekranów akustycznych
Projektowanie i budowa ekranów akustycznych stanowią kluczowe elementy dbania o komfort akustyczny w otoczeniu drogowym. Niestety, pomimo postępu technologicznego i dostępności zaawansowanych narzędzi projektowych, nadal często spotyka się błędy zarówno na etapie projektowania, jak i wykonawczym. W artykule przedstawiono najczęstsze z nich. Projektowanie i budowa ekranów akustycznych są kluczowymi elementami dbania o komfort akustyczny w środowisku drogowym. Jednakże nadal istnieją pewne pows...
Drony nad kopalniami. Nowa era pomiarów
Kolejne etapy prac Pierwszym etapem prac kameralnych jest obróbka zdjęć. Na wstępie korygowana jest kolorystyka zdjęć. Następnie oblicza się współrzędnemiejsca wykonania zdjęć i wprowadza się je do programu. Program w pierwszym kroku łączy zdjęcia. Co warte uwagi – im dokładniej znamy położenie każdego zdjęcia (pozycjonowanie drona za pomocą geodezyjnego odbiornika GPS), tym szybciej przebiega proces. Potem następuje wyrównanie sieci. Na tym etapie zawsze część fotopunktów pozostawiana jest j...
Ronda ‒ problematyka uszkodzeń nawierzchni
Wytyczne i realia użytkowania W obecnie stosowanych wytycznych do projektowania [7] znajdują się m.in. zapisy: „Szerokości jezdni i pierścienia ronda jednopasowego powinny zapewniać przejezdność pojazdu miarodajnego”. Zdaniem autorów, przyjmując założenie, że pojazd miarodajny (np. pojazd ciężarowy z naczepą) będzie poruszał się po przejezdnym pierścieniu, zgodnie z zapisami ustawy o drogach publicznych [9] należy uznać pierścień jako część jezdni przeznaczonej do ruchu. Takie założenie wynos...
Kraków: Tunel wzdłuż Opolskiej otwarty dla ruchu.
Od 22 maja tunel wzdłuż Opolskiej – jeden z najważniejszych obiektów inżynierskich budowanych w ramach linii KST III do Górki Narodowej – dostępny jest w całości dla kierowców. Ma dwie niezależne komory, każda po dwa pasy ruchu, jest długi na ok. 100 metrów, jest w stanie przyjąć pojazdy ważące nawet do 50 ton. Przypomnijmy: budowa tunelu rozpoczęła się w marcu 2022 r. od wykonania murków prowadzących dla ponad 60 tonowego dźwigu z wybierakiem. Maszyna sukcesywnie – metr za metrem – wybierała...
Kalendarium
Relacje
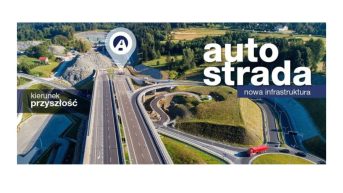
Spektakularne premiery produktów, osiem firm z nagrodami – za nami odnowiona formuła targów Autostrada Nowa Infrastruktura
54 firmy, m.in. z Polski, Malezji, Niemiec oraz Szwecji zaprezentowały...
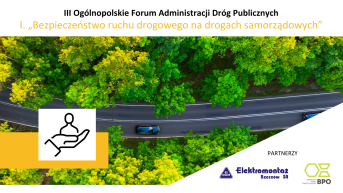
III Ogólnopolskie Forum Administracji Dróg Publicznych – Bezpieczeństwo ruchu drogowego na drogach samorządowych
4 kwietnia 2024 r. odbyło się pierwsze spotkanie III cyklu Ogólnopolskiego Forum Administ...
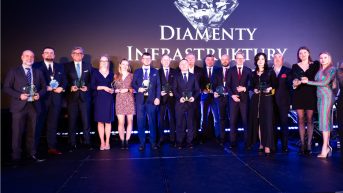
Relacja z XV edycji konferencji Infrastruktura Polska i Budownictwo
19 marca 2024 roku, w hotelu Sheraton Grand Warsaw, odbyła się XV jubi...