Maszyny do naprawy nawierzchni drogowej – rozkładarki mas mineralno-bitumicznych
Konstrukcja rozkładarki z podwoziem gąsienicowym (fot. 1) ujawnia swoje zalety nad grupą rozkładarek na podwoziu kołowym (oponowym), głównie przy pracy z większym obciążeniem. Zachowując lepszą stabilność, a co za tym idzie, dokładność rozkładania masy mineralno-bitumicznej, pozwala na podobne osiągi wydajności przy mniejszej prędkości jazdy roboczej. Napęd gąsienicowy wykazuje również mniejsze koszty utrzymania i konserwacji. Dodatkowo przedstawiono podstawowe problemy, które mogą pojawić się podczas pracy rozkładarki, ich przyczyny, a także sposoby ich usuwania zgodne z dokumentacją techniczno-ruchową wybranego modelu maszyny. Problemy te są w stanie zaistnieć pomimo skrupulatnego przestrzegania instrukcji obsługi w zakresie eksploatacji i konserwacji rozkładarki. Jednak dbałość o prawidłowe przebieganie tych procesów może pomóc zmniejszyć ryzyko ich wystąpienia lub wydłużyć czas przed ich zaistnieniem.
Ma to przede wszystkim bezpośredni wpływ na bezpieczeństwo osób obsługujących maszyn. Gdyż niweluje w dużym stopniu możliwość powstania usterki mogącej przyczynić się do bardziej złożonej awarii. Ponadto odpowiednie użytkowanie i utrzymanie rozkładarki pozwala uzyskać lepsze osiągi, czyli parametry rozkładania mas mineralno-bitumicznych. Tym samym zachowując wyniki pracy maszyny używanej porównywalne do nowego egzemplarza.
Eksploatacja i utrzymanie rozkładarek mas mineralno-bitumicznych
Przed przystąpieniem do użycia rozkładarki trzeba dokładnie sprawdzić jej stan oraz odpowiednio przygotować miejsce budowy. Należy również przestrzegać norm pracy rozkładarki, np. dotyczącej minimalnej temperatury powietrza do wbudowywania mieszanki mineralno-bitumicznej, według której nie powinno się układać żadnego rodzaju warstw przy temperaturze powietrza mniejszej niż 0°C [3].
Codziennie należy obejść rozkładarkę i sprawdzić: uszkodzenia części i oprzyrządowania, przecieki z silnika, układu hydraulicznego, przekładni itp., wszystkie punkty mocowań (podajnik zgrzebłowy, przenośnik ślimakowy, stół itp.). Stwierdzone usterki należy natychmiast usunąć, aby zapobiec uszkodzeniom, wypadkom lub skażeniu środowiska naturalnego.
Aby zapewnić rozkładarce pełną sprawność i gotowość do wykonywania pracy, konieczne są: przystosowanie stołu rozkładarki do pracy na żądanej szerokości, nastawienie żądanych parametrów pracy stołu roboczego (takich jak: profil poprzeczny stołu, skok i częstotliwość belki zagęszczającej oraz wibratora), ustawienie przenośników ślimakowych na odpowiednią wysokość ponad powierzchnię jezdni (wysokość ta powinna być taka, aby najniższy punkt ślimaka był o 50-75 mm wyżej od powierzchni zagęszczanej nawierzchni), zamocowanie czujników układu automatycznej niwelacji na rozkładarce i podłączenie ich do instalacji elektrycznej, ustawienie stołu roboczego na określoną grubość układanej warstwy (ustawienia dokonuje się najlepiej na dwóch drewnianych podkładach, grubość podkładów powinna być zwiększona o wielkość osiadania mieszanki przy jej zagęszczaniu), ustawienie kąta natarcia płyty gładzącej stołu, czyli kąta, jaki tworzy płyta gładząca stołu z podłożem (kąt zależy głównie od rodzaju mieszanki bitumicznej, prędkości jazdy roboczej rozkładarki oraz ciężaru stołu roboczego).
Konieczne są również: ustawienie czujników pochylenia wzdłużnego stołu do współpracy z zainstalowanym poziomem odniesienia układu automatycznej niwelacji, ustawienie wskaźnika kierunku jazdy rozkładarki, ustawienie wstępne wielkości prześwitu pod zasuwami dozującymi mieszankę, zamocowanie i wyregulowanie łączników krańcowych sterujących pracą układu podawania mieszanki, uruchomienie ogrzewania płyty gładzącej stołu [1].
Roboty drogowe
Podczas prowadzenia robót należy pamiętać o odpowiednim dostosowaniu temperatury mieszanki mineralno-bitumicznej oraz deski gładzącej stołu. Jak również prędkości jazdy do wydajności rozkładania mieszanki, szerokości rozkładania, przesuwaniu miejsc łączenia w przypadku układu wielowarstwowego (minimum 15 cm). Dodatkowo przy układaniu bardzo cienkich warstw (poniżej 2,5 cm) nie powinno się używać wibracji podczas zagęszczania. Grozi to rozgnieceniem ziaren. Jeśli podczas pracy rozkładarki za deską wibracyjną w układanej warstwie pojawią się bruzdy spowodowane ciągnięciem ziaren grysu, może to oznaczać, że układana warstwa jest zbyt cienka w stosunku do uziarnienia mieszanki. Lub też niedokładnie oczyszczono deskę rozkładarki lub ma ona zbyt niską temperaturę.
W przypadku tworzenia się fal na układanej nawierzchni przyczyny mogą stanowić: nierównomierne podawanie mieszanki, przejazd rozkładarki z niepełnym zbiornikiem, wadliwe podwieszenie stołu roboczego i błędy w jego ustawieniu, błędy w ustawieniu poziomu roboczego, uderzenia w rozkładarkę samochodu wyładowczego podczas napełniania zasobnika mieszanką bitumiczną. Powstanie szczelin jest natomiast spowodowane: zmianami w mieszance bitumicznej, wadliwą recepturą technologiczną, błędną temperaturą mieszanki, wadliwą grubością rozkładanej warstwy, małym zagęszczeniem podłoża i złą przyczepnością do niego rozkładanej mieszanki, zbyt krótkim przenośnikiem ślimakowym, zużytym stołem [1].
Mogą zainteresować Cię również
Wywiady
Waldemar Wojciechowski: Uczciwość to fundament etycznego zarządzania
Jakie są główne wyzwania związane z realizacją inwestycji drogowych w regionie Dolnego Śląska? Waldemar Wojciechowski: Główne wyzwania związane z realizacją inwestycji w regionie Dolnego Śląska wynikają ze specyfiki geograficznej, społecznej i gospodarczej oraz potrzeby intensywnego rozwoju infrastrukturalnego regionu. Zróżnicowanie ukształtowan...
Głosem branży: Innowacje i zrównoważony rozwój w wydobyciu kruszyw. Wyzwania i strategie dla przyszłości
W obliczu rosnącego zapotrzebowania na surowce budowlane, szczególnie kruszywa, kwestia efektywnego wydobycia oraz zarządzania zasobami naturalnymi staje się kluczowa zarówno w Polsce, jak i na świecie. Przemiany w tym obszarze nie tylko wpływają na gospodarki krajowe, ale także na środowisko, w którym eksploatacja surowców wiąże się z wieloma wyzwaniami, takimi jak zużycie energii czy generowanie odpadów. Poniżej przedstawiamy prognozy dotyczące przyszłości zasobów kruszyw oraz innowacje, kt...
Metoda oceny zabytkowej wartości obiektu mostowego – nie wszystko złoto, co się świeci
Wyznaczanie zabytkowej wartości punktowej obiektu Formularz do wyznaczania zabytkowej wartości punktowej obiektu mostowego przedstawiono w tab. 1. Kategoryzacja obiektu mostowego jako zabytku KATEGORIA I – ZABYTEK WYJĄTKOWY ΣP ≥ 80 Kategorię stanowią obiekty wyjątkowe, unikatowe i najcenniejsze, w których niczego nie można zmienić, należy tylko utrwalać ich istnienie. KATEGORIA II – ZABYTEK CENNY 80 > ΣP ≥ 50 Kategorię stanowią obiekty rzadkie i cenne, ...
Metody poprawy procesu przesiewania kruszyw
Proces przesiewania kruszyw odgrywa kluczową rolę w przemyśle wydobywczym i budowlanym, umożliwiając skuteczną separację materiałów ziarnistych według określonych frakcji. W wielu przypadkach użytkownicy maszyn przesiewających napotykają trudności związane z wydajnością i skutecznością tego procesu. Często nie jest konieczna całkowita wymiana parku maszynowego – istnieje szereg metod, które pozwalają na intensyfikację przesiewania przy niewielkich zmianach konstrukcyjnych i niskich kosztach. ...
Ocena przydatności kruszyw stosowanych do warstw podbudów drogowych na podstawie wybranych cech i własności mechanicznych
Znaczącym potencjałem użycia kruszyw alternatywnych jest drogownictwo. Zgodnie z Wymaganiami Technicznymi WT-4 [7] materiały ziarniste różnego pochodzenia mogą być wykorzystane na warstwy ulepszonego podłoża gruntowego, podbudowy czy nawierzchnie kruszywowe (fot. 1 i 2). Dopuszcza się stosowanie mieszanek o kontrolowanym składzie, klasyfikowanych jako [7]: a) mieszanka z betonu przekruszonego, b) mieszanka z przekruszonego muru, c) mieszanka z przekruszonego betonu i muru, d) przekruszone ma...
Szybka droga do bezpieczeństwa
Dodatkowe oznakowanie i pasy ruchu Nie wszystkie znaki drogowe wynikają bezpośrednio z przepisów. Często spotyka się oznaczenie numeru drogi na pasie, po którym porusza się kierowca. Jest to forma uzupełniająca, umieszczona na pasie, który rzeczywiście prowadzi w kierunku wskazanym tekstem, co pomaga kierowcy w wyborze trasy lub utwierdza go w dokonanym już wyborze. W przykładzie zaprezentowanym na fot. 4 widoczne są pasy z oznaczeniami S52 oraz A4 – kierowca, zbliżając się do łącznicy, odpow...
Geokrata. Jeden produkt, wiele zastosowań
Korzyści z użycia geokraty komórkowej Tomasz Herich, prezes firmy AG Geosynthetics sp. z o.o. Artykuł doskonale podkreśla kluczowe zalety geokraty komórkowej, która stała się nieodzownym elementem współczesnego budownictwa. Jako producent z wieloletnim doświadczeniem potwierdzamy: geokrata to rewolucja w stabilizacji gruntów, łącząca trwałość HDPE z ekologiczną efektywnością. Jej uniwersalność – od dróg po hydrotechnikę – wynika z elastyczności struktury, która nie tylko zwiększa nośność, ale...
Historyczny most kolejowy w Stanach k. Nowej Soli – 6 lat po remoncie i adaptacji na ścieżkę rowerową
Opis konstrukcji Most wykonano jako konstrukcję stalową, kratownicową, z pasami równoległymi (typu N) składającą się obecnie z 14 przęseł o łącznej długości 634 m (po odbudowie w 1955 r.). Wszystkie przęsła zaprojektowano jako belki swobodnie podparte na podporach murowanych z cegły klinkierowej, wzmocnionej blokami kamiennymi przeciwko działaniu kry. Podpory posadowiono na fundamentach betonowych na głębokości od 8,66 do 10,56 m poniżej poziomu gruntu. Oparcie przęseł na podporach zrealizowa...
Metody i systemy oceny stanu eksploatacyjnego jezdni drogowych
Wzrastające natężenie ruchu, utrata przepustowości dróg i zmieniające się relacje przewozowe sprawiają, że ograniczenie działań do samego utrzymania infrastruktury staje się niewystarczające. Konieczna jest rozbudowa sieci drogowej obejmująca poszerzenia nawierzchni, budowę dodatkowych pasów ruchu i likwidację skrzyżowań jednopoziomowych. W wielu przypadkach zachodzi potrzeba realizacji nowych tras, szczególnie dróg szybkiego ruchu. Budowa nowych odcinków dróg, obejść miejscowości i przełożeń...
Przygotowanie i wykonanie robót ziemnych oraz nawierzchniowych w budownictwie drogowym
Do produkcji mieszanek kruszywowych stosuje się różnorodne materiały, takie jak kruszywa naturalne, kruszywa łamane, żużle wielkopiecowe oraz ich mieszanki. Nowe regulacje pozwalają również na użycie surowców odpadowych, takich jak żużle hutnicze, łupki górnicze czy materiały z recyklingu, jak kruszywo betonowe i ceramika. Kluczową cechą dobrego kruszywa jest jego odpowiednie uziarnienie i właściwości mechaniczne. Aby uzyskać optymalne zagęszczenie, mieszanki powinny charakteryzować się ciągł...
Kalendarium
Relacje
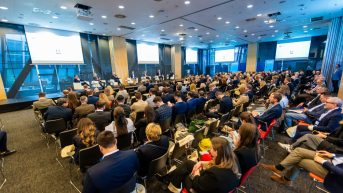
III Kongres Projektantów i Inżynierów
10 kwietnia 2025 r. w Centrum Konferencyjnym Centrum Nauki Kopernik w Warszawie odbył się...

IV Forum Dni Asfaltu
24–26 marca 2025 roku w Nałęczowie odbyło się IV Forum Dni Asfaltu, organizowane przez Po...
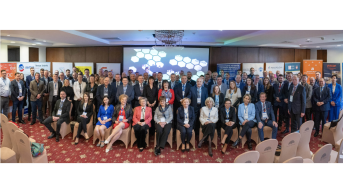
NOVDROG’25
10-11 kwietnia 2025 r. w malowniczych Niepołomicach odbyła się VII Ogólnopolska Konferenc...
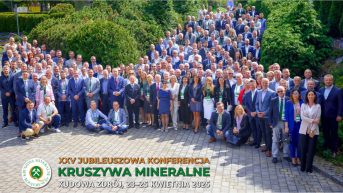
25 lat Konferencji KRUSZYWA MINERALNE Surowce – Rynek – Technologie – Jakość
Organizatorzy Od dwudziestu pięciu lat, począwszy od 2001 roku, Stowarzyszeni...